Chewing gum making plant
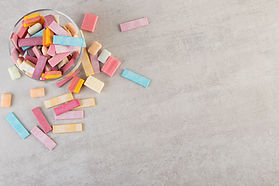
Dhiman engineers offers wide range of bubble gum production lines for various different styles and types of chewing gum products like bubble gum cut and wrap, bubble gum cut and fold style, chiclet type chewing gum, stick type chewing gum, ball type bubble gum.
Styles & Types
Dhiman engineers offers complete solution for gum manufacturing lines from mixers to final packaging
Dhiman Engineers have developed chewing gum making machines with different production capabilities for different types of consumer demand
Range Includes Laboratory scale models, startup production lines as well as high capacity production lines to fulfil all types of consumer's demand
Chiclet and stick chewing gum Process includes cooking, extrusion, pressing, rolling , forming, chilling , separating and packaging at the end.
Bubble gum cut and wrap machine is equipped with high grade mechanical parts and components which promises high durability and strength
Features Oil bath lubrication system which helps in high speed performance with noise free operation.
Smart Production Lines
Our Chewing gum production lines are One time investment
Which offers you with a lot of flexible business opportunities
Dhiman engineers offers continuous chewing gum processing lines which requires minimum human intervention
DE Smart production lines requires minimum labor to operate complete lines without any hassles
Which saves a-lot of labor wages and increase profit margin in production.
Machines are optimized to synchronize easily and deliver high speed production operations with minimum human intervene
Our chewing gum manufacturing machines are space saving, user friendly moreover easy to maintain, in order to give you trouble free years of production.
Dhiman engineers Bubble gum making machines are among one of the most reliable and economical production lines when it comes to after sale spares availability or keeping up with maintenance of the machines.
we work with an aim to Offer high performance international standard machines at fair prices with a motive to achieve milestone in installations
Chewing gum making machines can be easily customized to increase production capacity with minimum investment at any later stage which secures our customers investment and future.
Chiclet Chewing gum manufacturing machines includes pressing, rolling and cutting machines with water cooled pressing and cutting rollers which ensures unobstructed, seamless and continuous operation.
Safety and Health Assured
Chewing gum manufacturing machines features all safety features In order to maintain high level of
hygiene and product quality. All product contact parts are completely made of stainless steel and
other food grade materials which are easy to clean and rust free.
Our All Bubble gum making machines are designed and manufactured according to CE standards and FDA Regulations to follow high standard guidelines and to maintain high product quality and hygiene
All the electronic/electrical equipment are high rated certified and tested for safety and performance, follows high international standard CE guidelines to ensure maximum production output without any breakdown
On Site Assistance
we have served over 50 countries worldwide with our confectionery equipment
services, we have engineers who are expertise when it comes to whether on site or online
assistance to our customers with turnkey solutions.
Dhiman Engineers not only provide on site Successful trial Installations but also provide Skilled Machine operators for hire, which offers new business starters a lot of confidence and boost.
Dhiman engineers are always keen to overcome any objective to serve your need.
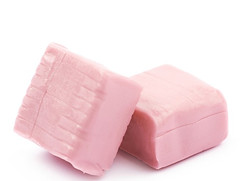

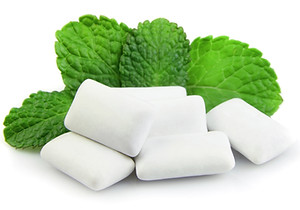

Two Color Bubble gum
Chiclet Chewing gum
Stick Chewing gum
Square shape
Bubble gum
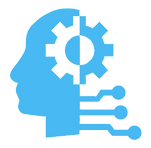
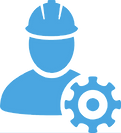
Cooking And Processing
Forming Section
Coating And Polishing
Technical data

PULVERIZER
(SUGAR GRINDER) - DPSG-200
Capacity
Dimensions (L X W X H)
Drive
Rotor speed (RAM)
Net. weight
100 Kg to 300 Kg According to product
700 X 1000 X 1700
3 HP AC
2800
350 kg.
Introduction:
Sugar grinding machine for food production is used to crush material into powder of 20-120 mesh. Used widely in pharmaceutical, chemical and food fields etc.
Principle and features:
By means of relative motion between movable and fixed plates, the material is crushed by the impact and friction of the teeth plate. Change the sieve to control the output size.
Sugar grinder machine has becomes the universal equipment especially used widely in sugar and salt production.
SIGMA MIXTURE - DSM-200
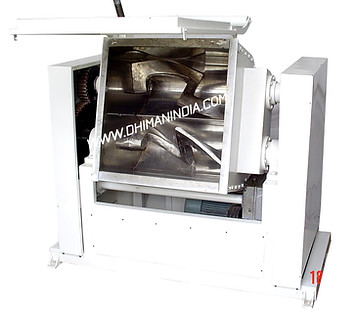
Application
Capacity
Drum Dimension (L X W X H)
Steam Working Pressure
Drive
Mixing
Tilting
Dimensions (L X W X H)
Weight
Manufacturing of Bubble Gum / Chew gum / Gum Base and final mixing of essence and color
200 Liters
760 X 760 X 760
60 Lb./Sq. Inch
10 H.P. A.C.
1 H.P. A.C
2000 mm X 1225 mm X 1325 mm
Net 1000 Kg.
Chewing gum making lines includes stainless steel double z sigma mixer with 200 L and 400 L capacity which offers various product mixing and cooking applications Is used for cooking of gum base and making bubble gum batch Features one push automatic tilting to discharge batch after cooking.
Heavy Duty steam Jacketed Bubble Gum Mixer is used to manufacture Gum Base, Bubble Gum and Chew gum material. If do not want to use steam then It takes about 6-7 hours to manufacture gum base. After manufacturing gum base, final mixing of color & essence is done in mixer which takes about half hour. Material can be discharged by tilting the mixer which is motorized operation.

TWIN COLOR ROPE EXTRUDER - DRX-150
Application
Capacity
Rope Diameter
Drive
Dimensions (L X W X H)
Weight
Rope forming of bubble gum or Chew-Gum material
1.2 Ton/Shif
According to requirement (Flat or Round)
5 HP AC
1225 mm X 1200 mm X 525 mm
Net 500 Kg
Bubble Gum Twin colour rope extruder is used to manufacture single or twin colour rope/sheet of required size or flat according to requirement from Bubble Gum or Chew-Gum material. The material is fed manually into the hopper and rope formed is collected in trays or discharged onto cooling conveyor
Gum extruders are available in twin screws as well as quad screws which varies in production capacities
Bubble gum extruders are optimized for manufacturing any style of bubble gum capable of extruding different shapes and sizes of gum ropes and sheets
Thanks to the water heated chamber which helps in keeping the batch warm for easy extrusion
Front face plate can be easily changed to change shape and size of rope or sheet according to final product.
multi Deck COOLING TUNNEL
DMC-7/11/13

Application
Capacity
Deck
Belt
Drive
Dimensions (L X W X H)
Cooling of Bubble-Gum Rope
600 kg / Hour
7/11/13 deck
250 mm wide (Food Graded non Sticky Belt)
3 H.P A.C. or D.C.
6000 mm X 1000 mm X 2000 mm
Seven deck cooling conveyor is used to continuously cool the rope coming out from the extruder. If you don't take this conveyor then the formed rope has to be kept in AC room for more than 4 hours. This conveyor makes the operation online and eliminates AC room. The conveyor has to be installed with air conditioner, which can be had from us or can be installed by you.
Bubble gum cooling tunnels are available in 7, 9 and 11 decks models according to production capacity of the line
Cooling tunnels are available with refrigeration system offering instant chilling effect to gum rope and sheets
Salient Features...
• All Side puff insulated.
• No need to use powder or Teflon non stick agents
• One cooling conveyor can handle up to three cut & wrap machines
• Other models also available with less/more number of belts and suitable for up to five cut & wrap machines.
Bubblegum CUT & FOLD WRAP - DFW-350

Application
Capacity
Product Size
Length Bubble-Gum
Width Bubble-Gum
Thickness Bubble-Gum
Wrapping Material
Dimensions (L X W X H)
Power
Drive
Heaters (Optional)
Weight
Gum Cutting & Fold Wrapping Machine
(Side Fold wrap)
300-350 PCs/Minute.
(Depending on Size of Bubble-Gum , wrapping and forming material used).
Length 20-30 mm.
Width 10-20 mm.
Thickness 6-12 mm.
Continues printed cellophane, Wax Paper, PVC (Non Magnetic) and Bopp, CPP, HM etc.
1750 X 915 mm X 1930 mm
500 Watts
2 H.P. (A.C or D.C.)
Net 1000 Kgs.
Bubble-Gum Cut & Wrap Machine automatically Cuts Bubble Gum and wrapping paper of the required size. Both these things are fed into a chamber where a twister twists or folds both sides of wrapping paper and wrapped product is discharged into a tray.
CHEWING GUM CUTTING MACHINE
DCC

Application
Capacity
Power Load
Drive
Dimensions (L X W X H)
Cutting/forming of chicklets, chewing gums
200 Kg per Hour
0.75 kW
2 H.P A.C. or D.C.
2000 x 700 x 1250 mm
Suitable for cutting chicklet, chewing gums of various sizes, with all contact parts of stainless steel.
.jpg)
REVOLVING COATING PAN
WITH HOT AIR BLOWER - DRp
Application
Available
Pan's RPM
Heater Capacity
Motor
Blower Motor
Pan Mounting Angle
Net Weight
Sugar Coating Pharmaceutical Tablets
30" / 36" / 42" / 48" / 60" PAN DIA
22 R.P.M
1.5 KW
(According to Size of Pan) III PH / 440V/AC
0.25 H.P. / III PH/440V/AC
Standard Angle 600 (According to requirement)
(According to size of Pan)
Coating Pan revolves by motorized oil bath gear box with hot air (adjustable) blower. The pan is made by 304 quality stainless steel (adjustable) blower. The pan is made by 304 quality stainless steel (can be provided S.S. 316 quality at extra cost).
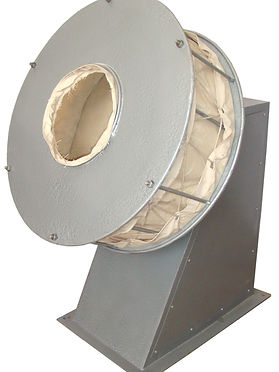
POLISHING REVOLVING PAN - dprp
Application
Available
Pan's RPM
Motor
Pan Mounting Angle
Net Weight
Polishing Chewing gums, Chiclets ,Pharmaceutical Tablets
36" Inch
22 R.P.M
1 H.P. III HP / 440 V/AC
Standard Angle 60
250 Kg
It is basically used for Polishing Chewing gums, Chiclets, Pharmaceutical tablets
INFO
Dhiman Engineers provides a wide selection of bubblegum-making machine, from sugar batching and dissolving to syrup processing, as well as mass boiling, chilling, dragging, rope sizing, moulding, bundling, and packing. What could a person seeking for bubble gum producing machines possibly require now that we've presented them with a one-stop shop
Since the first bubblegum was introduced to the public, bubblegum gum production has progressed dramatically. The core activities of the process of production, however, remain the same and may be classified as follows: mixing the materials; shaping the bubble gum mass; cooling the bubblegum; cutting the lozenges into individual components; and packaging the product. Every one of those phases varies based on the type of gum being produced and the many engineering improvements that have occurred in the machinery employed in a certain industry. Being the best gum making machine
This chewing gum making machine manufacturer is primarily designed for chewing gum and bubble gum manufacture. A completely automatic manufacturing line including a blender, a twister, a roll and scoring machine, a cooling conveyor cabinet, and a gum wrapping machine is included in the apparatus. It has the ability to make sweets in a variety of forms. The entire system is highly automated, dependable in manufacturing, versatile, and simple to use. It's the greatest material for chewing gum and bubble gum manufacture.
A bubble gum-making machine may be operated at a reasonable price. Because it can function autonomously, this equipment may also help you save money on recurrent labour expenditures. Furthermore, a gum-making machine will cost less to set up, maintain, and run. New variations of gummy items may be made with gum making equipment. By using many colours, two-fold layers, and focus filling, the machine can make the bubblegum appealing to the marketplace. You can even reduce your investment by upgrading the gum-making equipment to manufacture various gum candy.
As this chewing gum making machine is self-contained once programmed, no or few personnel are needed. All you have to do now is programme the gum-making machine to meet your demands. It has a great production capacity due to its totally automated nature.
This type of gum-making equipment needs some great work. For example, for it to function properly, it requires regular human involvement. Semi-automatic gum-making machines are available in a wide range of sizes, energy requirements, output volume, and operating conditions. Semi-automatic gum-making machines may be suited for small-scale or large-scale manufacturing due to a variety of characteristics. Furthermore, compared to fully automated bubblegum-making machine, they have a lower output capacity.
You will prepare all of the components for the gum at the very first step. Ascertain that all of the machine's components are in proper operating order. To make gum, you must thoroughly combine all of the materials. In certain cases, you can process the gum base while mixing the components in the first stage. Warming, swirling, and melting are used to combine the ingredients in the combining tanks. Furthermore, you have the option of combining the materials in batches or continuously. The warmth used to mix the components in the tank is affected by the mixing option you choose. Culturally homogenous mixes result in a thick molten syrup, which may be used in chewing gum making machine.